揚(yáng)州不銹鋼光亮盤管簡(jiǎn)介
不銹鋼盤管在焊接前首先管子材料必須采用機(jī)械加工的方法進(jìn)行管段截取,端面不可用燃?xì)飧畹堕_坡口或加工焊接表面。焊接端口必須無缺陷,毛刺、碎屑應(yīng)清除,背面不得有倒角。接頭兩側(cè)20mm范圍內(nèi)氧化物必須清除干凈。必須采用專用不銹鋼刷子清除工作表面的氧化物(不銹鋼刷子不能在碳鋼上使用,以免產(chǎn)生污染)。其次,不銹鋼盤管內(nèi)需要充氬氣。具體做法是在焊前,將木制堵板加在盤管焊口的附近兩側(cè),形成隔離充氣小室(一般把堵板放在離焊口各100~150mm處),一端向充氣室充氣,并從另一堵板中心小孔出氣,為了減少管內(nèi)氬氣從對(duì)口間歇處流失,降低保護(hù)效果,焊接前可沿焊口間隙貼上膠帶,邊焊接邊揭去膠帶。為了補(bǔ)充氣室漏去的氬氣,焊接全過程都應(yīng)不間斷的向管內(nèi)充氬,氬氣流量應(yīng)適當(dāng)。流量過小,氬氣保護(hù)不好,焊縫背面容易氧化。流量過大,焊接時(shí)產(chǎn)生渦流帶入空氣,保護(hù)效果也會(huì)變壞,同時(shí)會(huì)引起焊縫的根部?jī)?nèi)凹等缺陷,影響焊接質(zhì)量。一般充氬流量控制在6~8L/min。另外應(yīng)特別注意的是,應(yīng)該在充氣時(shí)將充氣室或管內(nèi)空氣排凈后,焊接才能進(jìn)行,否則影響焊接質(zhì)量。局部充氣方法:堵板制作要求在焊接前將兩塊堵板事先放置于管子的兩側(cè),扣好繩子,焊接完成后,把兩塊堵板從管內(nèi)抽出。
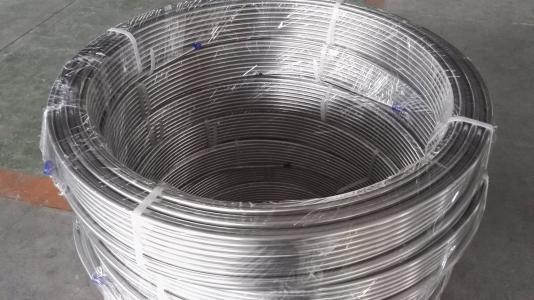
揚(yáng)州不銹鋼光亮盤管知識(shí)
焊接過程控制
焊接過程中控制好焊接變形,要嚴(yán)格選擇焊接方法和工藝參數(shù),要利用焊接構(gòu)件實(shí)際特點(diǎn)為前提進(jìn)行焊接方法的選擇。比如將跟蹤激冷、隨焊兩側(cè)加熱、碾壓等方法使用到焊接過程中,這樣更好的將焊接變形問題控制好,利用隨焊兩側(cè)加熱技術(shù)能夠均勻分布縱向應(yīng)變,促使殘余應(yīng)力降低,和隨焊兩側(cè)加熱技術(shù)相比較,隨焊碾壓要具有特殊設(shè)備進(jìn)行幫助,存在比較大的使用限制。焊接的過程中,為了更好的將焊接變形控制好,要重視焊接人員實(shí)際的業(yè)務(wù)能力提高,要按照工藝方案嚴(yán)格設(shè)定工藝參數(shù),嚴(yán)謹(jǐn)隨便更改焊接工藝參數(shù),保證操作人員嚴(yán)格進(jìn)行操作規(guī)定,另外定期對(duì)焊接人員進(jìn)行培訓(xùn),完善焊接工作者的知識(shí),讓所有焊接人員進(jìn)行實(shí)踐操作經(jīng)驗(yàn)的分享。經(jīng)過焊接的三個(gè)環(huán)節(jié)的對(duì)應(yīng)的控制處理工作,挑選恰當(dāng)?shù)姆桨,?shí)現(xiàn)全方位的控制焊接變形,才可以保證將焊接工藝給不銹鋼盤管帶來的變形問題抑制。
揚(yáng)州不銹鋼光亮盤管新聞
制造檢驗(yàn)工藝方案及其質(zhì)量控制
制造難點(diǎn)
該設(shè)備外形尺寸比較大.同時(shí)帶有夾套,雙層內(nèi)盤管,盤管接頭處焊接的難度較大.按照設(shè)計(jì)要求,設(shè)備內(nèi)筒要進(jìn)行氣密性試驗(yàn),所以對(duì)整個(gè)制造及檢驗(yàn)提出了較高的要求。由于容器夾套封閉件較多,且封閉件處的接管不僅與內(nèi)筒焊接還與內(nèi)部的兩層盤管焊接.因此給制造帶來很大的困難。
封頭及筒節(jié)的成型
(1)上、下封頭材料為06Cr19Ni10不銹鋼板.由于尺寸較大封頭用板采用板料拼接后整體旋壓成型.拼接焊縫進(jìn)行100%射線檢測(cè)lI級(jí)別合格,成型后內(nèi)里她光處理。上封頭成型后最小厚度4.15mm.下封頭成型后最小厚度12mm
(2)內(nèi)筒程筒節(jié)的加工.按照常規(guī)的制造加工工藝進(jìn)行,筒節(jié)經(jīng)內(nèi)壁拋光處理、滾圓、焊接、校圓。無損檢測(cè)合格。
(3)夾套封頭材料為Q345R不銹鋼板,板料拼接后整體旋壓成型.拼接焊縫進(jìn)行20%且長度不小于250mm射線檢測(cè)Ⅲ級(jí)合格。成型后最小厚度5.5mm