不銹鋼無(wú)縫盤(pán)管簡(jiǎn)介
不銹鋼盤(pán)管在焊接前首先管子材料必須采用機(jī)械加工的方法進(jìn)行管段截取,端面不可用燃?xì)飧畹堕_(kāi)坡口或加工焊接表面。焊接端口必須無(wú)缺陷,毛刺、碎屑應(yīng)清除,背面不得有倒角。接頭兩側(cè)20mm范圍內(nèi)氧化物必須清除干凈。必須采用專用不銹鋼刷子清除工作表面的氧化物(不銹鋼刷子不能在碳鋼上使用,以免產(chǎn)生污染)。其次,不銹鋼盤(pán)管內(nèi)需要充氬氣。具體做法是在焊前,將木制堵板加在盤(pán)管焊口的附近兩側(cè),形成隔離充氣小室(一般把堵板放在離焊口各100~150mm處),一端向充氣室充氣,并從另一堵板中心小孔出氣,為了減少管內(nèi)氬氣從對(duì)口間歇處流失,降低保護(hù)效果,焊接前可沿焊口間隙貼上膠帶,邊焊接邊揭去膠帶。為了補(bǔ)充氣室漏去的氬氣,焊接全過(guò)程都應(yīng)不間斷的向管內(nèi)充氬,氬氣流量應(yīng)適當(dāng)。流量過(guò)小,氬氣保護(hù)不好,焊縫背面容易氧化。流量過(guò)大,焊接時(shí)產(chǎn)生渦流帶入空氣,保護(hù)效果也會(huì)變壞,同時(shí)會(huì)引起焊縫的根部?jī)?nèi)凹等缺陷,影響焊接質(zhì)量。一般充氬流量控制在6~8L/min。另外應(yīng)特別注意的是,應(yīng)該在充氣時(shí)將充氣室或管內(nèi)空氣排凈后,焊接才能進(jìn)行,否則影響焊接質(zhì)量。局部充氣方法:堵板制作要求在焊接前將兩塊堵板事先放置于管子的兩側(cè),扣好繩子,焊接完成后,把兩塊堵板從管內(nèi)抽出。
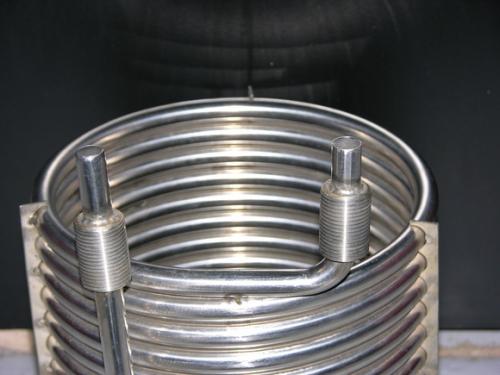
不銹鋼無(wú)縫盤(pán)管知識(shí)
不銹鋼盤(pán)管生產(chǎn)完畢檢驗(yàn)合格后,在進(jìn)行裝配前,應(yīng)清除管子坡口邊緣的水、污油、油漆及其它臟物。盤(pán)管對(duì)接裝配時(shí),要對(duì)準(zhǔn)其內(nèi)管壁錯(cuò)位不得超過(guò)最大不超過(guò)1mm。為了保證自熔質(zhì)量,自熔時(shí)管子內(nèi)和熔極處均須通氬氣保護(hù),管子內(nèi)其裝置定位焊由持證焊工焊,焊材與正式焊縫使用的一致,定位焊質(zhì)量要求與工件焊縫的相同,高度與寬度不得超過(guò)正式焊縫,反面成形與焊縫一致。定位焊上如有缺陷要將其打磨掉,決不能留在焊縫中,定位焊應(yīng)不少于三點(diǎn),定位焊長(zhǎng)約10mm左右。
為了保證不銹鋼盤(pán)管與閥門(mén)接頭焊接質(zhì)量,避免出現(xiàn)上述焊接缺陷,浙江有限公司對(duì)初始接頭結(jié)構(gòu)做了優(yōu)化設(shè)計(jì),加工一根過(guò)渡短管,管長(zhǎng)10mm,其外徑與接頭相同,內(nèi)徑與盤(pán)管的口徑相同,在端面上加工一臺(tái)階,尺寸為Φ4×1mm,臺(tái)階高度為0.5mm;待焊不銹鋼盤(pán)管插入過(guò)渡管內(nèi),端面高出臺(tái)階1mm。
不銹鋼無(wú)縫盤(pán)管新聞
制造檢驗(yàn)工藝方案及其質(zhì)量控制
制造難點(diǎn)
該設(shè)備外形尺寸比較大.同時(shí)帶有夾套,雙層內(nèi)盤(pán)管,盤(pán)管接頭處焊接的難度較大.按照設(shè)計(jì)要求,設(shè)備內(nèi)筒要進(jìn)行氣密性試驗(yàn),所以對(duì)整個(gè)制造及檢驗(yàn)提出了較高的要求。由于容器夾套封閉件較多,且封閉件處的接管不僅與內(nèi)筒焊接還與內(nèi)部的兩層盤(pán)管焊接.因此給制造帶來(lái)很大的困難。
封頭及筒節(jié)的成型
(1)上、下封頭材料為06Cr19Ni10不銹鋼板.由于尺寸較大封頭用板采用板料拼接后整體旋壓成型.拼接焊縫進(jìn)行100%射線檢測(cè)lI級(jí)別合格,成型后內(nèi)里她光處理。上封頭成型后最小厚度4.15mm.下封頭成型后最小厚度12mm
(2)內(nèi)筒程筒節(jié)的加工.按照常規(guī)的制造加工工藝進(jìn)行,筒節(jié)經(jīng)內(nèi)壁拋光處理、滾圓、焊接、校圓。無(wú)損檢測(cè)合格。
(3)夾套封頭材料為Q345R不銹鋼板,板料拼接后整體旋壓成型.拼接焊縫進(jìn)行20%且長(zhǎng)度不小于250mm射線檢測(cè)Ⅲ級(jí)合格。成型后最小厚度5.5mm